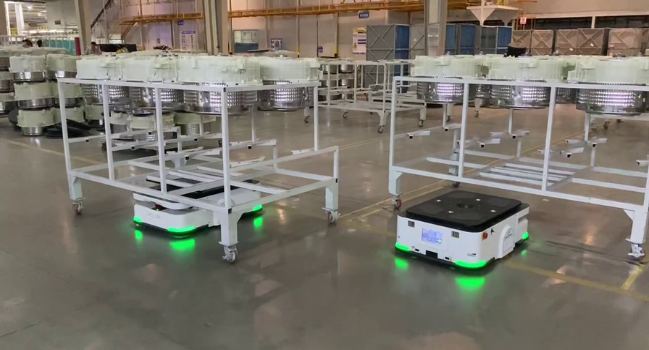
As the pace of smart living in the appliance industry continues to accelerate, appliance manufacturers must increase investment in flexible production equipment to respond to rapidly changing needs.
This renowned appliances manufacturer has joined with Standard Robots to build an intelligent logistics project in the manufacturing industry based on our flexible AMR solution and expand the application of smart manufacturing technology in the appliance industry.
Automation, Informatization, and capacity balance
Autonomous mobile robots (AMR) Oasis 600UL have improved productivity, safety, and balanced production fluctuations within a laundry machine factory. "Every 45 minutes to an hour, workers had to spend 10 minutes or more moving trolleys and waiting between lines due to the production capacity differentiation between IronWoker station and the final assembly line. We want Oasis AMRs to regulate the production variation and release people from moving materials from place to place." Senior Production Manager of the factory.
The solution was to focus on building two WIP line-side storages that can process up to 4000 laundry machine barrels in a 20 hours shift which automatically balanced the production fluctuations between the stamping process and final assembly. Therefore, 5 OASIS 600UL mobile robots were deployed to transport 100 custom roller racks of WIP from ironworkers machines to the line-side storage area, and two AMR to automate the transportation of line-side WIP to the final assembly.
With smart navigation technology, combined with software intelligence
The five Oasis 600UL mobile robots were equipped with advanced laser SLAM technology to give a 360° field of view for maximum safety and to blend in with the factory's dynamic environs. Additionally, the range of the front 3D cameras extends 30 meters above the ground to allow the robot can see the rack and other obstacles that are typically challenging for other robots to perceive, thanks to multiple sensors on each side.
Through 5G connectivity, Standard Robots Fleet Management System (FMS) manages all the 600UL between the existing production management software. By integrating the APS, WMS, and FMS for overall production management and control, production profits are increased, more assertiveness is achieved in a shorter time, more data and analysis are available, and reduced production errors.
Future intelligent material handling with mobile robots
In the beginning, the company most interested in the Oasis 600UL AMRs was their reliability and scalability, as they intended to implement them as an alternative to solve production capacity differentiation between the two processes. However, the intention was quickly changed thanks to the positive experience the manufacturer has had so far with AMRs.
They are currently examining the potential of deploying more Oasis mobile robots on a wider scale for processes they now carry out manually using forklifts and people who push roller racks in other areas of the factory floor.