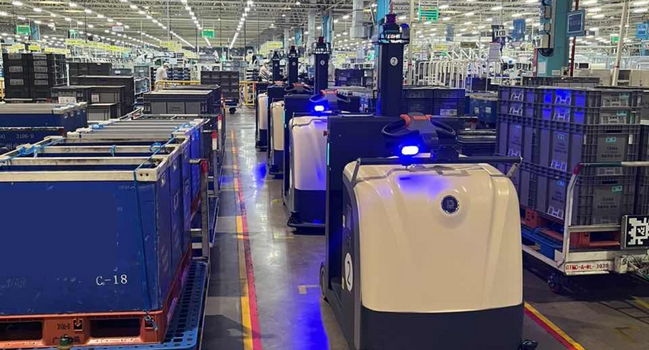
An automobile final assembly workshop is the single largest production hall in a car factory. The production line orchestrates over 3000 components and assembles 20 to 40 cars per every hour. Because of high value demands, the last 100 meters of the car parts staging area became critical for feeding the assembly line on time as well as efficiently. Also, the free-up human resources can be reconverting back into productive tasks and join with Toyota’s long term sustainability goal.
Solution
It seemed only logical for Toyota to automate internal material flows for the assembly line using robotics solutions. The Gulf 3000 smart tractors were carefully picked from all the available options in the mobile robot market due to the heavy-duty features, flexible control system with our structural changes to the existing infrastructure and could be deployed quickly.
The six Gulf-3000 operates in a fully automated setup with multiple trolley attached as an autonomous logistic train. The factory workers now pack the trolleys for the Gulf-3000 with all components and parts for the final assembly line in an optimized timeline, so all the components that needed are always ready at the right time. On this basis, The Gulf Smart Tractors keeping the stock low, less car parts, and saving a lot of space for sudden changes of workflows, also ensuring the lean principles.
Automatic Towing Connection
The Gulf-3000 operates based on the SLAM technology, which fuses data from the robot’s onboard sensors and processes that use computer vision algorithms to "recognize" features in the surrounding environment. Using SLAM technology as its foundation, the robot can quickly detect the physical location of the trolley and attach the rear hook using a visual scan. The Smart Tractor "knows" the fastest way to get to the destination independently and efficiently. Lastly, the Gulf-3000 is capable of towing these trolleys and moving up to 3 tons per trip. The robots travel between each production hall and make each stop autonomously, using the Fleet Management System to communicate with gates and section doors.
Safer and More Flexible Working Fonditions
Once the basic setup and mapping tasks are completed, employees on the factory floors can easily master how to schedule the tractors every day using FMS. The software not only manages robots and communicates with factory WMS, but it also tracks real-time status and visualizes data. These features allow employees and operators to gain more clear situation awareness for better decision making. While people are interested and willing to work with technology that improves their daily jobs, the actual safety in manufacturing facilities can be improved by robots as well. The Gulf-3000 smart tractor is well equipped with multiple safety functions, such as 360° full-area obstacle avoidance, spatial 3D obstacle avoidance, emergency kill buttons, and sound and light alarms are integrated.